Machine Condition Monitoring of CNC Machines
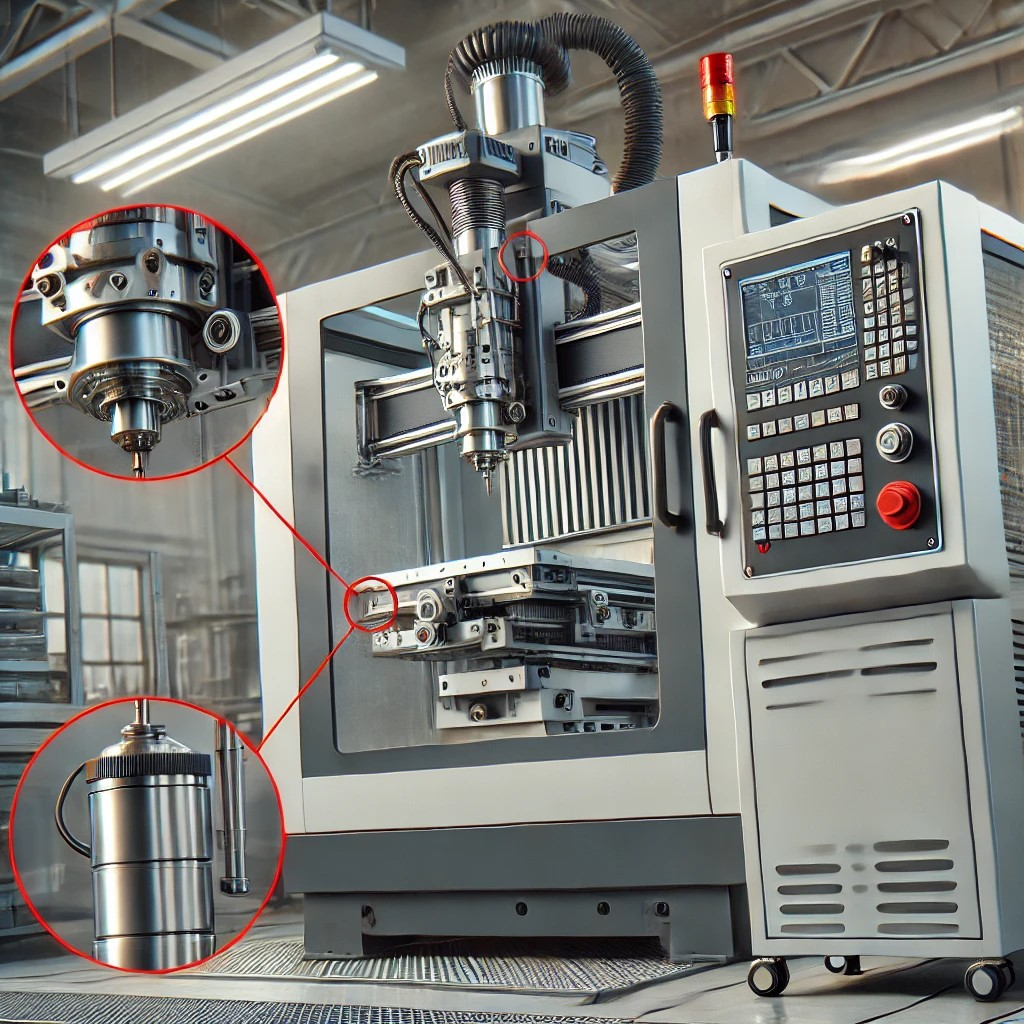
Machine Condition Monitoring (MCM) is crucial for maintaining the efficiency and reliability of Computer Numerical Control (CNC) machines. These machines are integral to modern manufacturing, enabling precision and automation. We explore the methods, benefits, and challenges associated with MCM in CNC machines, emphasizing the role of various monitoring techniques and technologies in enhancing machine performance and reducing downtime.
Computer Numerical Control (CNC) machines are pivotal in manufacturing sectors, facilitating precise control over machining processes. However, like all mechanical systems, CNC machines are susceptible to wear and tear, which can lead to malfunctions and production halts. Machine Condition Monitoring (MCM) offers a solution by providing real-time insights into the machine's health, allowing for predictive maintenance and reducing unexpected failures .
Methods of Machine Condition Monitoring
- Vibration Analysis:
Vibration analysis is one of the most widely used techniques for monitoring the condition of CNC machines. It involves measuring the vibration signals of machine components to detect abnormalities. Changes in vibration patterns can indicate issues such as imbalances, misalignments, or bearing faults. - Thermal Monitoring:
Thermal monitoring involves using infrared cameras and temperature sensors to detect overheating in machine components. Abnormal temperature rises can signify excessive friction, lubrication failures, or electrical issues, which can lead to component degradation. - Acoustic Emission (AE) Monitoring:
AE monitoring detects high-frequency sound waves generated by crack formation or other mechanical changes in materials. This technique is particularly useful for detecting early-stage damage in critical components, enabling timely maintenance actions. - Oil Analysis:
Oil analysis examines the lubrication oil for contaminants and wear particles. The presence of specific particles can indicate wear in particular components, such as gears or bearings, providing insights into the internal condition of the machine. - Current and Power Monitoring:
Monitoring the electrical parameters such as current and power consumption can reveal issues in the electrical and mechanical systems of CNC machines. Abnormal power usage patterns often indicate underlying mechanical problems or inefficiencies.
Benefits of Machine Condition Monitoring
- Enhanced Reliability:
MCM helps in identifying potential issues before they lead to machine failures, thereby enhancing the overall reliability of CNC machines. This proactive approach ensures consistent machine performance and product quality. - Reduced Downtime:
By predicting failures and scheduling maintenance activities during non-productive hours, MCM significantly reduces machine downtime. This increases the overall efficiency of manufacturing operations and reduces production costs. - Cost Savings:
Preventive maintenance based on MCM data can lead to substantial cost savings. It helps avoid expensive emergency repairs and extends the lifespan of machine components, reducing the need for frequent replacements . - Improved Safety:
Monitoring critical machine parameters ensures that any dangerous conditions are detected early, preventing accidents and ensuring a safer working environment for operators .
Challenges in Machine Condition Monitoring
- Data Management:
The vast amount of data generated by various monitoring systems can be overwhelming. Efficient data management and analysis are crucial for extracting meaningful insights and making informed maintenance decisions. - Integration with Existing Systems:
Integrating MCM systems with existing CNC machine controls and enterprise resource planning (ERP) systems can be challenging. Ensuring seamless communication between different systems is essential for effective monitoring and maintenance planning - Initial Investment:
The initial cost of implementing MCM systems can be high. This includes the cost of sensors, data acquisition systems, and analytical software. However, the long-term benefits often justify the investment . - Technical Expertise:
Effective MCM requires specialized knowledge and expertise in both the monitoring techniques and the specific machinery being monitored. Training personnel and developing this expertise can be resource-intensive.
Machine Condition Monitoring is a critical aspect of modern CNC machine maintenance, offering numerous benefits including enhanced reliability, reduced downtime, and cost savings. Despite the challenges associated with data management, system integration, and initial investment, the advantages of MCM make it an indispensable tool in the manufacturing industry. Future advancements in sensor technology and data analytics are expected to further enhance the effectiveness and accessibility of MCM systems.
This is where we can help with such challenges! To learn more about our Machine Condition Monitoring solutions, contact us.